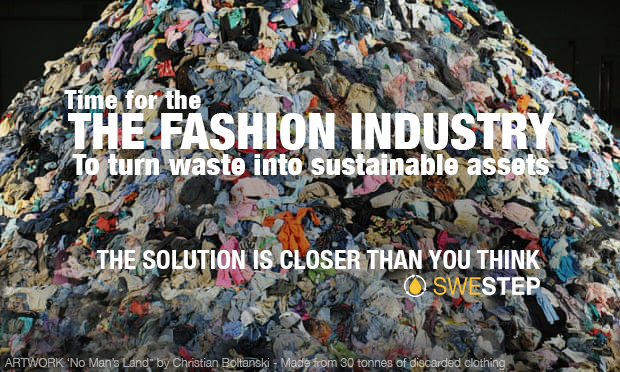
Lack of clear definitions in the issues related to “RECYCLING” has for many years created misunderstandings and confusion in the industry.
A general perception is still that the term recycling is identical to mechanical recycling (including reusing), both based on a separation process, where everything must be put into different waste streams…
– This is neither viable nor sustainable that so much of the waste (especially textile residues) ends up in landfills or sent for incineration.
In order to succeed in achieving set climate goals, the market needs access to alternatives to mechanical recycling, as it has its limitations and is both time-consuming and expensive.
“Feedstock Recycling”, a broader form of “Chemical Recycling” must be seen as an sustainable alternative, it is one of the most profitable and flexible recycling solutions on the market, seen from both input material (feedstock) and end products.
Swestep offers a Game Changing Catalytic Conversion Process (“Feedstock Recycling Technology”) that can recycle all hydrocarbon based waste into a Fossil Free, CO2 Neutral Synthetic Oil. A solution where fossil-dependent industries can become fossil-independent in a viable environmental and profitable way.
FASHION FACTS – Fast fashion makes shopping for clothes more affordable, but it comes at an environmental cost, and a large share of the 150 billion garments that are produced each year go to waste.
– The fashion industry produces 10% of all humanity’s carbon emissions
– Is the second-largest consumer of the world’s water supply
– And pollutes the oceans with micro plastics.
– So, time for change
– Time to take the next step
#Swestep – Next Generation Recycling Technology
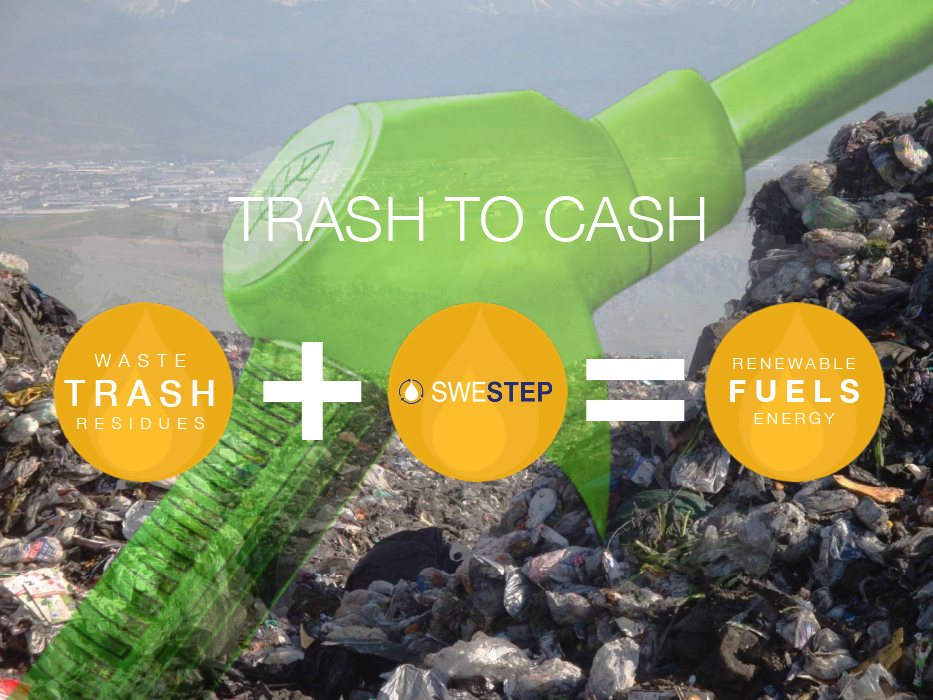
SWESTEP is poised to deploy its innovative SWESTEP Plants, representing the forefront of process technology in sustainable recycling production. This game-changing technology unlocks enormous market potential for sustainable production, breaking free from the shackles of conventional fossil energy sources.
SWESTEP delivers a capital-efficient, profitable solution that thrives in any setting, whether small-scale or large-scale, and regardless of customer profile, community size, or geographic location.
The demand for renewable fuels and sustainable liquids used to produce climate friendly products is global scaled. Since the Industrial revolution, production of greenhouse gases and toxic chemicals have escalated tremendously, which has resulted in an urgency to replace fossil fuels with renewable alternative.
The United Nations and the European Union are pushing hard with directives to accelerate the adoption of renewable fuels.
SWESTEP – Turning Waste into Wealth
The Future is Now – Time to Break the Mold
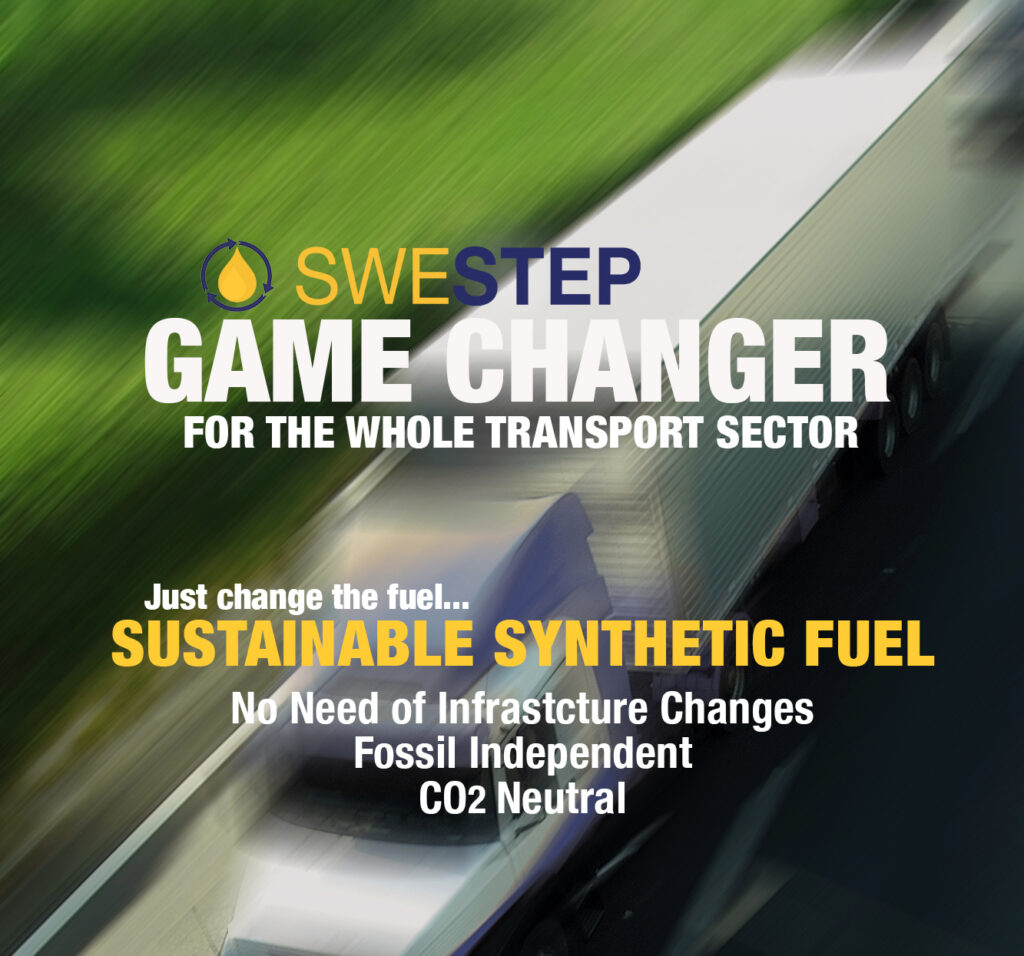
The Transport Sector is in the middle of a transformation paradigm where decision-makers are negatively affected by strong lobbying activities. In order to make sustainable and long-term decisions, a holistic view is required
– The solution is closer than you think – Renewable Synthetic Fuels
Heavy vehicles have a life cycle of at least ten years, and often longer than that. The entire logistics industry faces an extensive challenge if we are unable to run vehicles on sustainable fuels for their full service life. An effective conversion is therefore both about achieving the goal of electrification but also about finding effective solutions for the least possible climate impact on the way there.
With a long-term perspective on the environment and climate, Sweden as a nation should ensure that we can use the vehicles that roll on our roads during their full life. The vision of a complete transition to electric power for heavy vehicles on our roads before 2040-2050 is greatly exaggerated.
In order to cope with the transition to greener transport on land, air and sea the public sector needs to met with a stable and secure infrastructure for heavy transport for both today’s and tomorrow’s vehicles. Otherwise we risk missing the target.
All fuel and engine alternatives must be considered before deciding what to prioritize and support by decision makers.
The choice of which road to take / decide is of utmost importance to be able to make a sustainable transition to a fossil-independent transport sector and circular society.
The solution is closer than you think.
SEE LINK “Swestep-The Game Changer“
SWESTEP – Next Generation Recycling Technology
Swestep’s CC process (Catalytic Conversion Process // Feedstock Recycling and Energy Recovery) is a sustainable recycling solution for the production of renewable synthetic fuels.
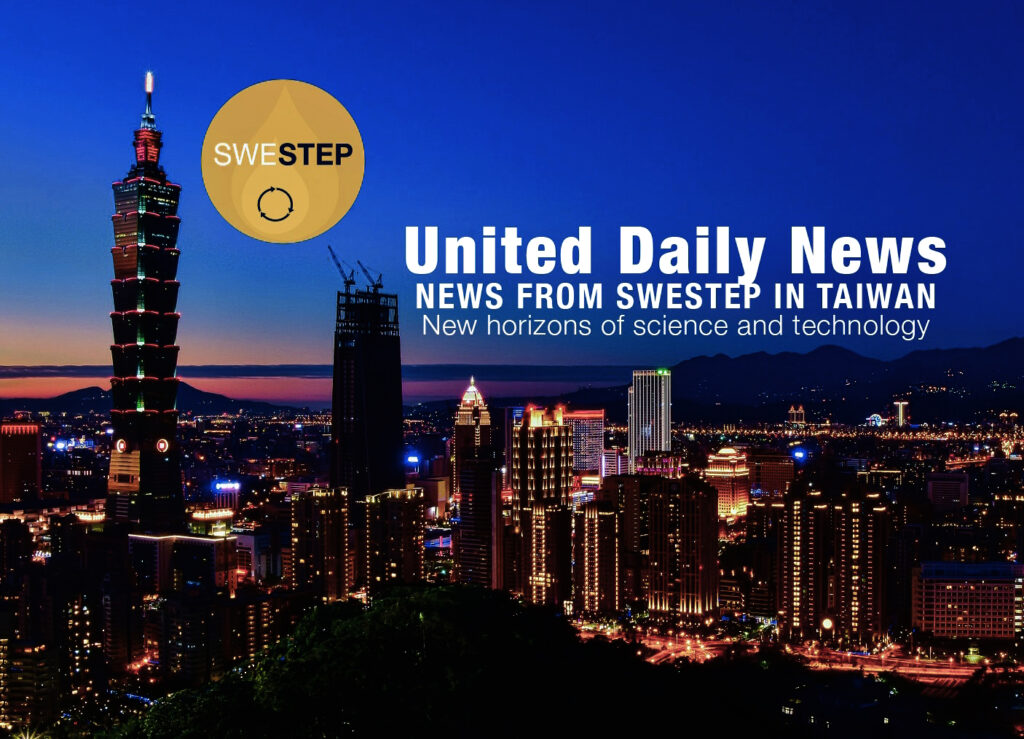
SWESTEP – Chemical Transformation and Recycling Technology Boosts Corporate ESG Development
SOURCE; Link to original article from United Daily News in Taiwan
In the era of carbonomics, experts predict that carbon will become the third currency of the market, in addition to the US dollar and the Chinese yuan. Mr. Huang Jieping, CEO of Greatech Technology, said that Sweden has the highest carbon tax in the world, up to 122 euros per ton, which puts huge pressure on enterprises but also cultivates world-class carbon reduction capabilities. Greatech has introduced SWESTEP’s sustainable technology of chemical transformation and recycling from Sweden to help enterprises promote ESG (Environmental, Social, and Governance).
Greenhouse gases mainly come from fossil fuels, and coal combustion emits a large amount of carbon. Converting coal into oil is a good idea, but the cost of producing clean coal is too high. Data shows that Taiwan’s annual carbon emissions are about 280 million tons, of which Formosa Petrochemical Corporation alone accounts for 25 million tons, and with the affiliated companies in the group, the total accounts for nearly 20%. Although Yunlin County’s income is not high, its carbon emissions are not small, and Mailiao bears a significant responsibility. Groups such as Formosa Plastics, Uni-President, Evergreen, and China Steel actively seek carbon reduction solutions, and all have shown interest in SWESTEP and are carefully evaluating it.
SWESTEP can recombine the carbon and hydrogen molecules of seven recycled plastics into hydrocarbon bonds, producing naphtha oil that is similar to crude oil and can be further processed into chemicals such as ethylene. The conversion rate of SWESTEP is 85%, and the production cost of 1 liter of synthetic biodiesel is 0.5 euros, which can be as low as 0.3 euros for large-scale equipment. The residual 3% mineral salt residue can be used as fertilizer, achieving true zero-waste circular economy. One liter of this type of biodiesel can generate 5-10 degrees of electricity, and the cost of electricity generation per degree is even lower than nuclear energy, Huang Jieping said.
Large carbon emitters and the capital market are highly interested in SWESTEP. SWESTEP’s fully automated pre-processing process consists of 11 procedures and can run 24 hours a day. With a total cost of 20 million euros (about 660 million Taiwan dollars) for the complete set of equipment in the middle and later stages, the equipment can produce 1 ton of diesel per hour, and the estimated IRR of small and large equipment is 29% and 45%, respectively, with a recovery period of 5.5 years or 3.5 years. The negative pressure smokeless chimney equipment covers an area of 200 pings, including a total of 1,500 pings in the surrounding area. Compared with incinerators, it occupies several hectares of land. In Penghu, with a daily garbage output of 72 tons, only one set of equipment is needed.
Energy independence and security are crucial for island economies, and Taiwan is no exception. In the early stage, Greatech Technology aimed at Penghu and used SWESTEP to achieve a low-carbon island. The main benefits come not only from the processing fee but also from the renewable energy and carbon credits generated. Huang Jieping said that Japan exports technology and funds to Myanmar and the world through the Joint Crediting Mechanism (JCM) of carbon credits, following this model. There are more than 50,000 islands around the world, and international funds, including Saudi Arabia’s basic industry, are optimistic. Japanese venture capital, H & Q Asia Pacific, which was approved by the National Development Council at the end of last year, are sharpening their swords.
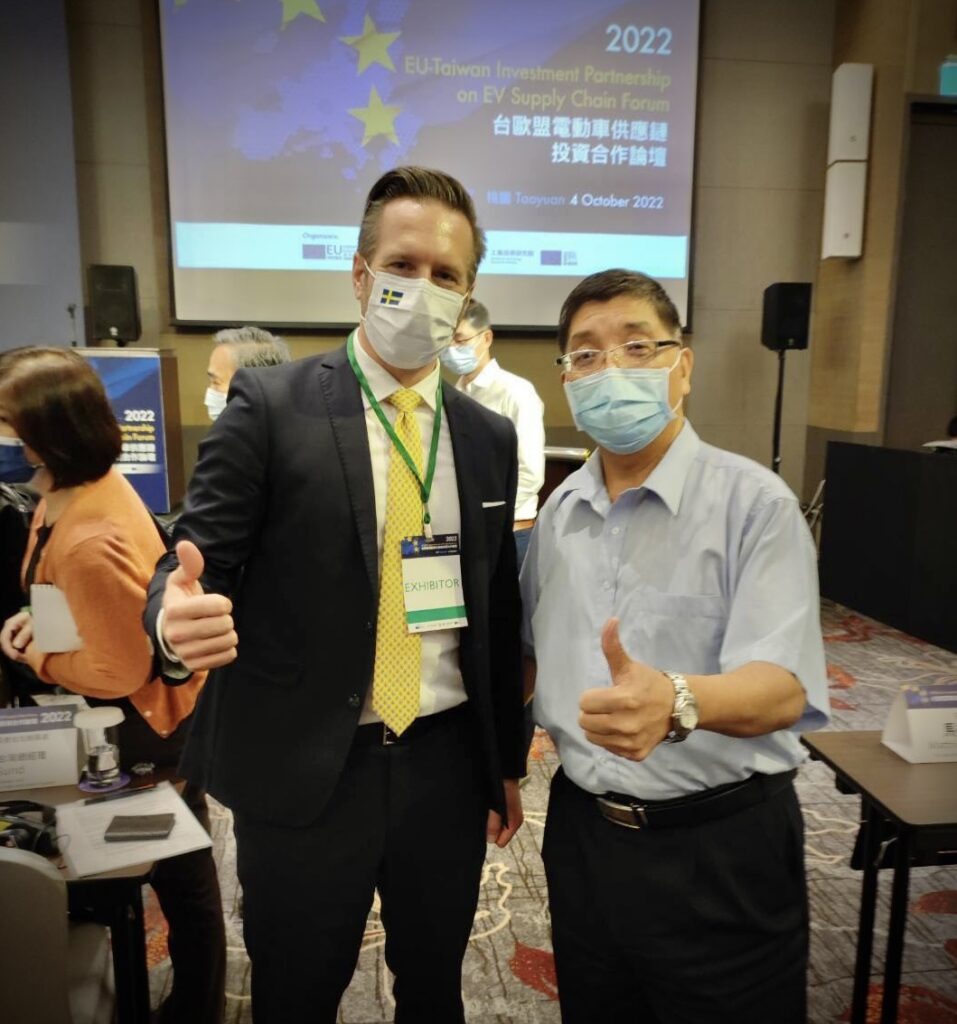
Mr. Huang Jieping together with Petter Sund, General Manager of Taiwan and Director of the Business Division of the Swedish Trade and Investment Council, at the Taiwan-EU Electric Vehicle Supply Chain Investment Cooperation Forum last year.
SOURCE; Link to original article from United Daily News in Taiwan
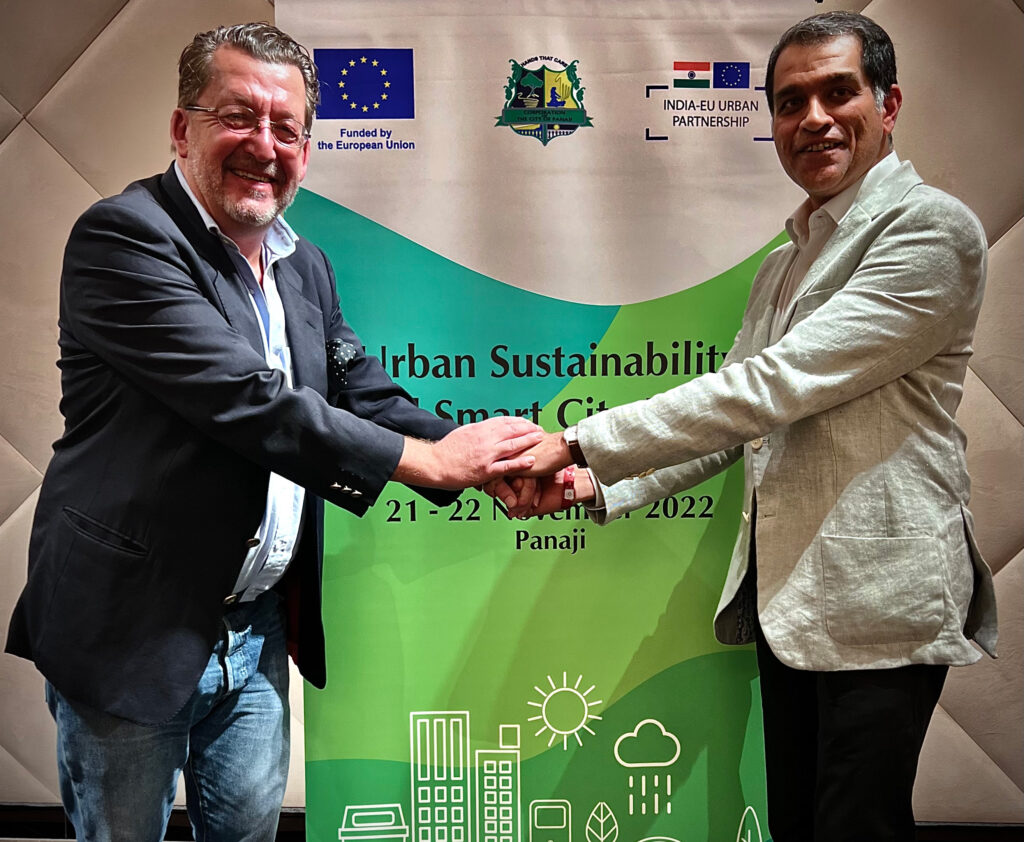
JP Morgan Friberg represented Swestep as speaker in Panaji, Goa India at the conference “URBAN SUSTAINABLE and SMART CITY EVENT”, where waste management was high on the agenda.
The conference was interesting, uplifting and productive, among the participants were decision-making politicians, university and several companies in the private sector working with waste management, infrastructure and urban planning.
INFORMATION – The Urban Sustainability and Smart City (USSC)
The USSC Event is a series of 4 events conducted under the India – EU Urban Partnership (IEUP), a project between the Ministry of Housing and Urban Affairs, Government of India, and the European Union, to support the implementation of smart, resilient and sustainable urban development in India.
On the agenda on the USSC Event was; developments in the areas of mobility, solid waste management and urban resilience. The event was facilitated by the AETS-IEUP project team over two days and have participants from the public and private sector from India and the EU.
LINK to EU News
SWESTEP will exhibit at PLASTIC NORDIC / MALMÖMÄSSAN: 10-11 MAY 2023 – WELCOME!

The entire value chain of the Nordic plastic and rubber industry gathers here!
The industry is in constant development and many polymeric materials can now be recycled and contribute to a circular economy.
Plastteknik Nordic is the obvious meeting place for you who work as a designer, develop or manufacture products in polymeric materials. Update yourself on sustainable material solutions for future design, product development and manufacturing. Book your visit to Plastteknik Nordic today!
New technology and new production methods are a crucial part of the future of the plastics and rubber industry.
Welcome!!
Check this link for more information