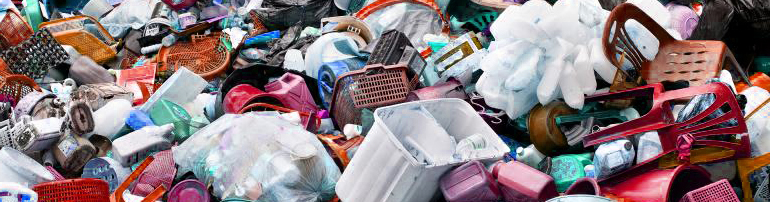
MAKE PLASTIC WASTE USEFUL
– Plastic could be Fantastic – If made Circular and Sustainable with clear rules, laws and requirements about where and how it must be recycled –
The industry and decision makers have to rethink how their value plastic and polymeric products and see it as a circular material. The responsibility for producing, handling and recycling, from a product life cycle perspective – must be put on the producer. They are the ones who push prices, margin and pollutes our oceans, water and land.
PLASTIC FEEDSTOCK – Time to give plastic waste a value, price and meaning… See plastic waste and residues as a non fossil feedstock to be recycled into renewable fuels for the transport sector or virgin grade recycled material for the chemical industry to refine into performing chemicals for all fossil dependent industries.
SOLUTION PROVIDER – A SWESTEP Plant can recycle/turn all organic hydrocarbon-based waste and residues, including plastic, into renewable fuels (for Air-Land-Sea) or additives and virgin raw oils to refine into performance chemicals for the petrochemical industry. (New Raw materials that can help fossil dependent industries close the loop for future production of plastic, textile, cosmetic, medicine glue and binding materials)
SWESTEP intends to develop and roll out their technology on an industrial scale as it has the potential to:
• Recycle plastics for which there are limited other viable and effective recycling solutions and technologies today.
• Remove all undesired substances in the process.
• Produce virgin grade oils, sustainable additives and renewable fuels
• Turn biomass and solid waste/residues into valuable feedstock for the chemical industry or fuel for the transport sector.
SOLUTION PROCESS – Through the patented *CC process, plastic waste is broken down to fuels, oil or gaseous liquid products for the chemical industry. These hydrocarbon-based materials (feedstock) could replace todays fossil feedstock and be used to produce new sustainable and circular products, plastic being one segment among others.
THE CC TECHNOLOGY – A SWESTEP Plant – The Next Generation Process Technology for Sustainable Recycling Production.
– No high temperatures creating cancerogen materials and gases
– Low pressure -0.05 bar
– Co2 neutral
– High efficiency
– Great variation on insert material
– Great variation on the end product
– Circular economy
– Co2 Neutral economy
– Strengthens the local and regional independent of oil import
– No greenhouse gases from production
Time to leave the fossil dependence
Time to take the next step
SWESTEP
*CC = Catalytic Conversion Process
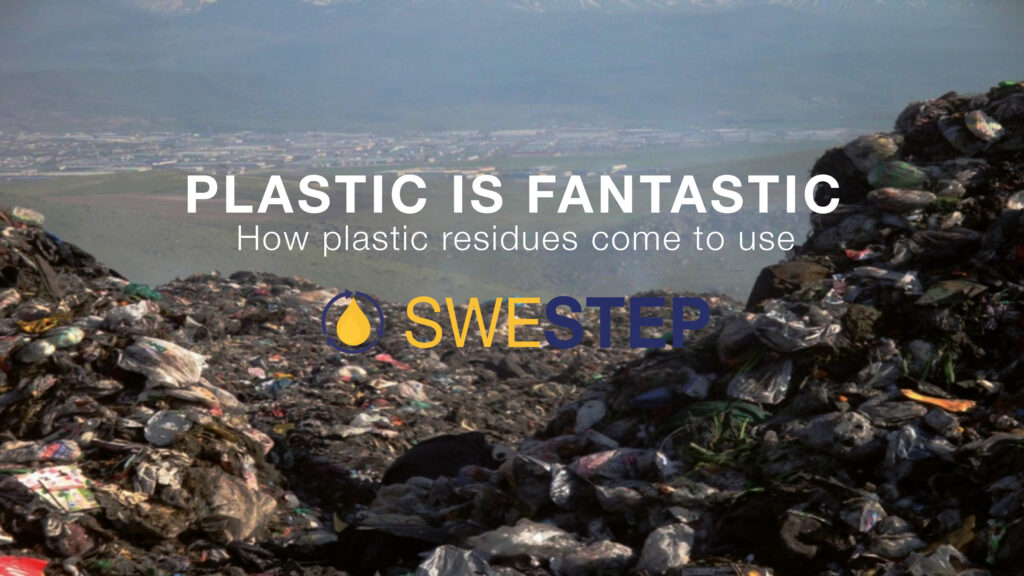
Plastic is Fantastic…
If made Circular and Sustainable with clear rules, laws and requirements about where/how it must be recycled
Today, most of all plastic waste goes to incineration and only a minor part is mechanically recycled. In addition, mechanical material recycling gives plastics a lower quality than the original.
Therefore, it is important to highlight feedstock recycling as a justifiable and profitable alternative for industry to produce green plastic products with guaranteed quality that meet the sustainability and environmental requirements.
Swestep’s CC Process is an efficient method for plastic recycling, the waste can be broken down at molecular level and deliver an oil product that can be refined into performance chemicals and/or new optional plastic products that meets the industry quality requirements.
– Another advantage of Swestep’s technology is that it also allows a gradual phase-out of fossil dependence.
Plastic waste recycling is poised to be the most important and transformative trend in the petrochemicals industry during the coming decade. Replacing plastic with other materials is not practical. When considering all aspects of the product lifecycle, plastics have a much lower environmental cost than their alternative materials.
So, while opportunities exist to reduce per capita plastic consumption, the solution to plastic waste must include the ongoing use of plastics for their superior material properties.
The end products are renewable fuels, energy and/or a chemical raw material (in liquid form) that can be processed into performance chemicals and new materials for all fossil-dependent industries.
Important to emphasize is that Swestep’s patented CC process (Catalytic Conversion Process) mimic natures decay process, but in contrast to that it takes nature millions of years Swestep’s solution do it under 6 minutes.
The technology is a combined feedstock-, chemical-, and mechanical recycling process that can recycle all hydrocarbon-based waste and residues. (Including contaminated waste, end of life products and flame retardant material)
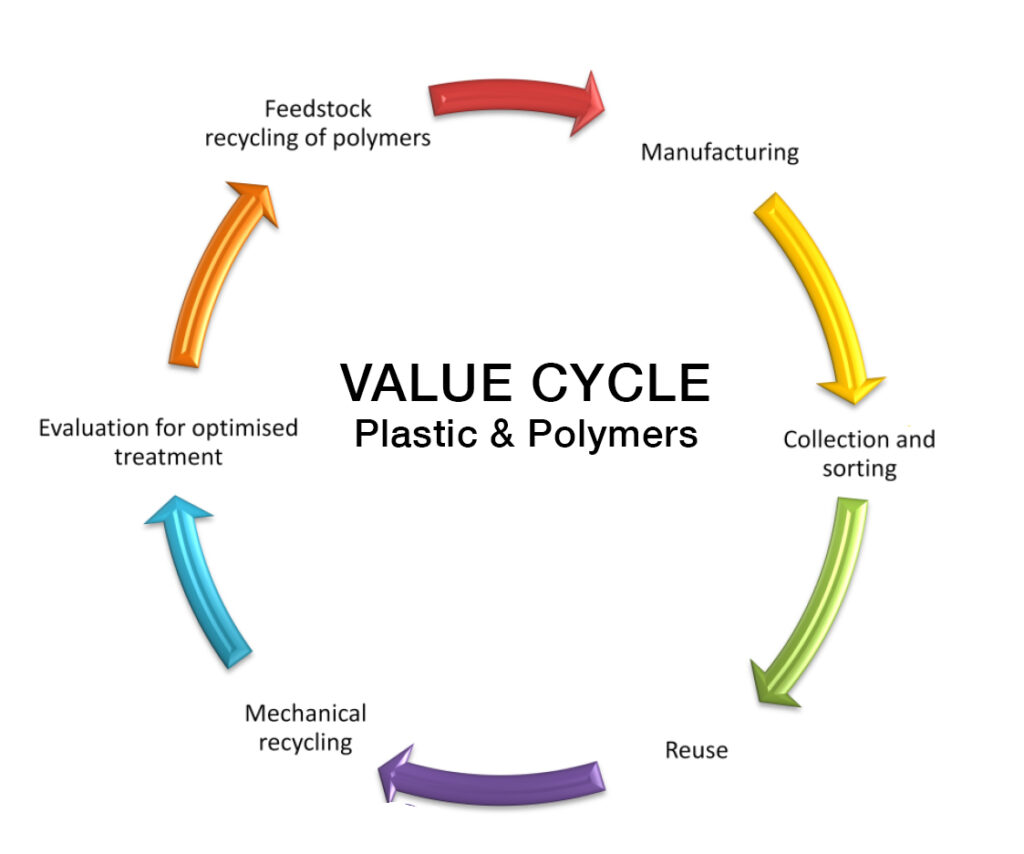
Priority is given to circularity, and therefore it is graded in the following order;
1. Reuse, 2. Mechanical Recycling, 3. Feedstock Recycling. However, all solutions have their pros and cons. – Quality requirements, handling, sorting, cost, time, profitability and environmental impact.
INFORMATION – The CC process is NOT an incineration technology – There are no chimneys; Thanks to that the production process runs under 300°C there are no cancerogenic (Furans, dioxins…) emissions produced.
Time to take the next step
Time for change
Swestep – All residues come to use