Swestep acquires new patents that will revolutionize production of fossil-free fuels
Swestep announces that they have acquired four patents for technology that will revolutionize the production of fossil-free fuels.
These four patents enables a more efficient production of renewable fuels from waste from paper and biomass and other organic waste including plastics, using Swestep’s CC technology.
– Swestep’s technology and the patents we have acquired mean that it is now possible to extract more renewable energy from waste from the paper and pulp industry than before. In addition, the investment cost is a fraction compared to what alternatives in the market require. This is an unbeatable combination, fully in line with what we have previously offered to handle other organic waste and plastics for other fossil-dependent industries globally, ”says Karl-Magnus Mattsson, CEO and founder of Swestep.
The basic function of CC technology is to convert organic waste, such as lignin, into a liquid end product which can be used directly as fuel or chemical raw material to refine into performance chemicals for the production of plastic, textile, glue or cosmetics. The oil can also be used as raw material for further processing – for example in the form of hydrogenation / additives to conventional diesel.
Through the process combinations that the patent covers, an efficient production of renewable fuels is obtained from primarily wood raw materials, including related waste such as lignin. The tests conducted with lignin show high cost efficiency.
– The Swestep process produces a liter of diesel from three kilos of lignin and biomass. It blends into one third each of non-recyclable plastics and cardboard products, which otherwise are burned up, with the biomass we get 1 liter of diesel from about 2.5 kg of waste, says Karl-Magnus Mattsson.
The first deliveries of customer facilities are expected to be up and running in 2020. Two of these plants are planned to be built in Sweden.
Link to original artikel in swedish
_____________
The SWESTEP process technology can effectively recycle all hydrocarbon-based waste, including plastic, into renewable additives and fuels for Air-Land-Sea or a virgin sustainable raw oil to refine into liquids or performance chemicals for the petrochemical industry. (Raw materials/liquids that can help fossil dependent industries close the loop for future production of textile, cosmetic, medicine and plastic)
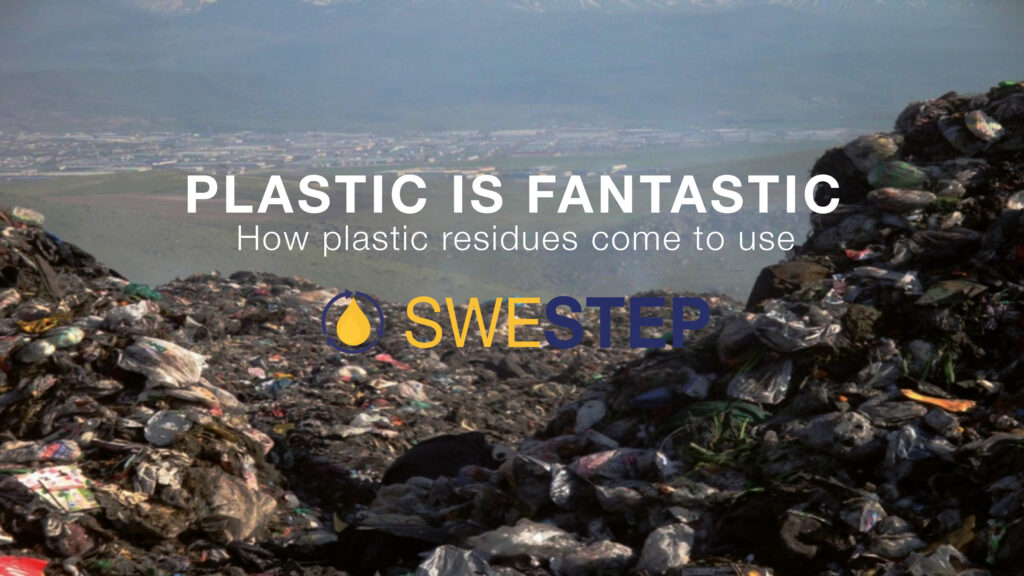
Plastic is Fantastic…
If made Circular and Sustainable with clear rules, laws and requirements about where/how it must be recycled
Today, most of all plastic waste goes to incineration and only a minor part is mechanically recycled. In addition, mechanical material recycling gives plastics a lower quality than the original.
Therefore, it is important to highlight feedstock recycling as a justifiable and profitable alternative for industry to produce green plastic products with guaranteed quality that meet the sustainability and environmental requirements.
Swestep’s CC Process is an efficient method for plastic recycling, the waste can be broken down at molecular level and deliver an oil product that can be refined into performance chemicals and/or new optional plastic products that meets the industry quality requirements.
– Another advantage of Swestep’s technology is that it also allows a gradual phase-out of fossil dependence.
Plastic waste recycling is poised to be the most important and transformative trend in the petrochemicals industry during the coming decade. Replacing plastic with other materials is not practical. When considering all aspects of the product lifecycle, plastics have a much lower environmental cost than their alternative materials.
So, while opportunities exist to reduce per capita plastic consumption, the solution to plastic waste must include the ongoing use of plastics for their superior material properties.
The end products are renewable fuels, energy and/or a chemical raw material (in liquid form) that can be processed into performance chemicals and new materials for all fossil-dependent industries.
Important to emphasize is that Swestep’s patented CC process (Catalytic Conversion Process) mimic natures decay process, but in contrast to that it takes nature millions of years Swestep’s solution do it under 6 minutes.
The technology is a combined feedstock-, chemical-, and mechanical recycling process that can recycle all hydrocarbon-based waste and residues. (Including contaminated waste, end of life products and flame retardant material)
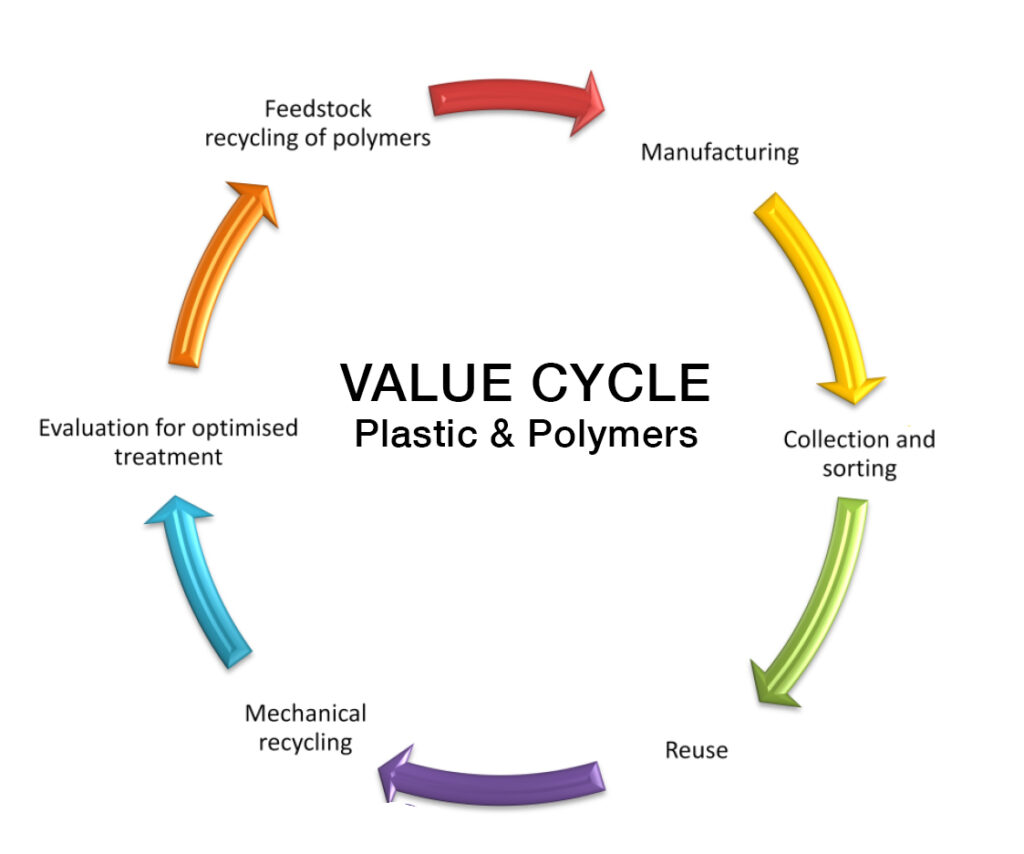
Priority is given to circularity, and therefore it is graded in the following order;
1. Reuse, 2. Mechanical Recycling, 3. Feedstock Recycling. However, all solutions have their pros and cons. – Quality requirements, handling, sorting, cost, time, profitability and environmental impact.
INFORMATION – The CC process is NOT an incineration technology – There are no chimneys; Thanks to that the production process runs under 300°C there are no cancerogenic (Furans, dioxins…) emissions produced.
Time to take the next step
Time for change
Swestep – All residues come to use